About Us
Unogiochi, exclusive brand of the Iamtoys Srl company, began more than 30 years ago, with the purpose of producing a selection of traditional games and toys revised and updated for today's market.
Since the mid-19th century, the Iovane family had been making the famous Panariello (basket for the Neapolitan Tombola game) in a completely artisanal way, which they still carry on as a tradition.
In the 90s, the business felt the need to industrialize and enter the large-scale distribution market, thus becoming one of the leading toy manufacturers in Italy and internationally with 3 production plants covering over 30,000 sqm.
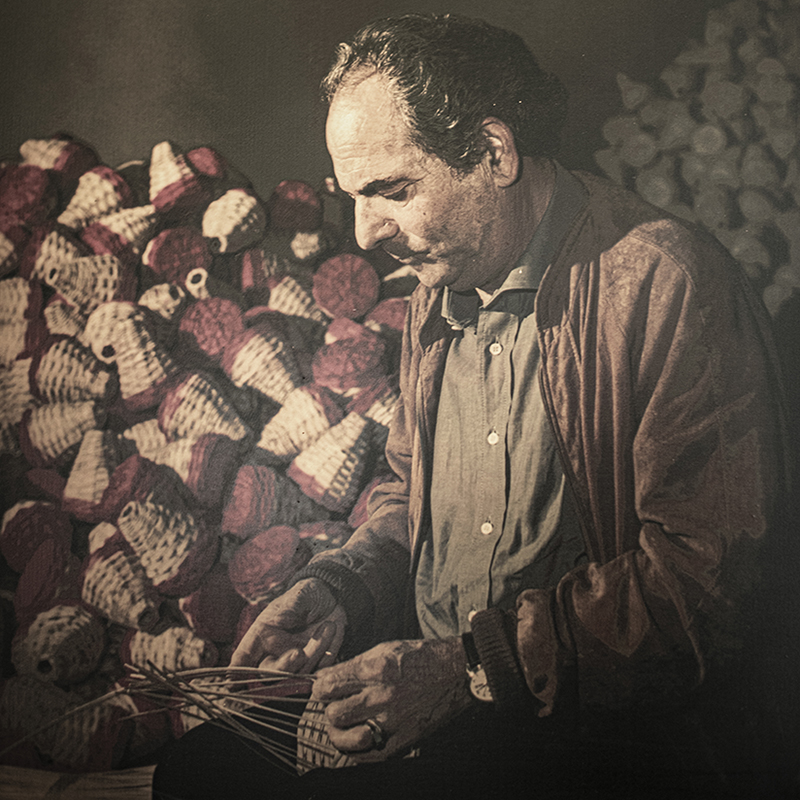
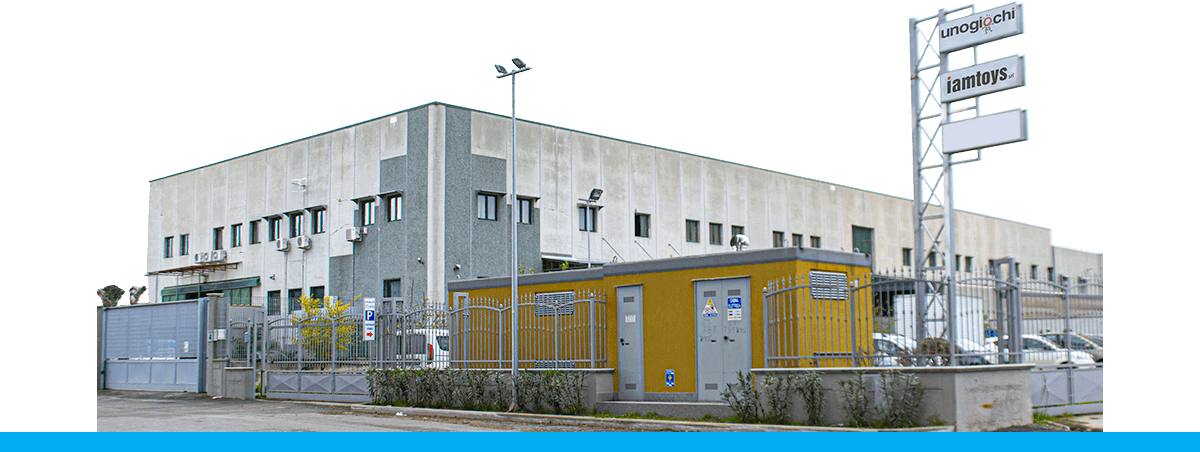
Mission
Games are a tool through which kids develop ethical knowledge, such as minding rules and respecting other players, or relational skills, like socializing, teamwork, sharing, and cognitive skills, like creativity, attention, memory and logical thinking.
The aim is therefore to provide every child with products to have fun and stimulate their creativity.
Production process
Our plastic manufacturing process uses various tools that shape and color the base polymers into final shapes.
In fact, the design process is a complex activity, which requires the use of machinery specialized in processing materials.
Polymer coloring via masterbatch
Pellets of polymers such as polypropylene and HDPE (High-Density Polyethylene) are basically transparent. To give the color, therefore, a mixing process is used together with a resin-based mix with a high concentration of pigments and additives called Masterbatch.
Masterbatches are ideal for coloring plastic products, and are nowadays widely used; they are used for coloring industrial equipment, household appliances, fabrics and packaging, up to design and commonly used objects and, of course, also toys.
The masterbatch is mixed with the pure polymer pellet during the processing of the material (for example, during molding) to allow easier addition of additives, which would otherwise be added in powder form with consequent difficulty in both dosing and mixing. Particular attention must be paid during this phase, to ensure adequate dispersion of the pigment and allow homogeneous coloring of the polymer.
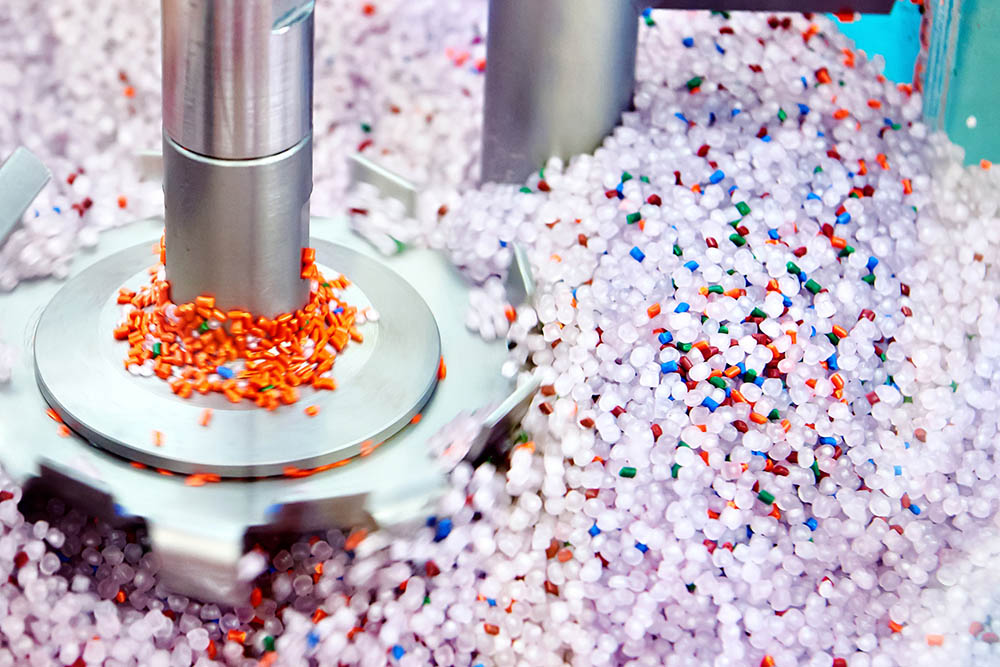
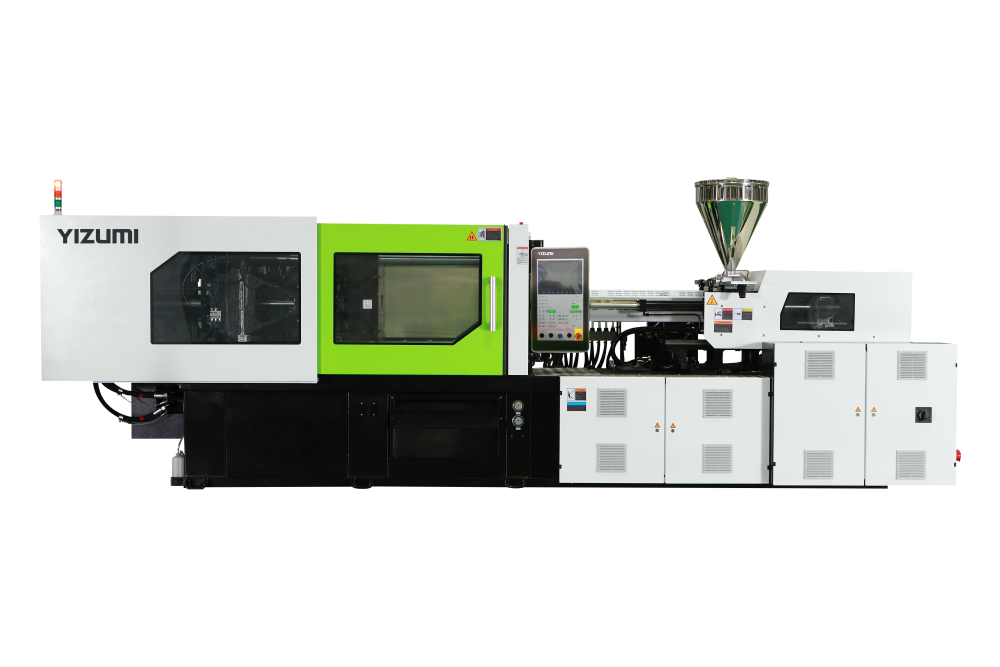
Injection molding
Plastic injection molding involves melting polypropylene pellets which, once they have become sufficiently malleable, are injected under pressure into a closed mold designed to reproduce the desired shape.
After designing the mold, the plastic is introduced in the form of pellets into the press, where the polymers will melt inside it. Once the casting process is complete, the liquid plastic is injected into the mold, and after cooling and solidification, the finished, molded part is ejected.
Thanks to the machinery we use, such as the Yizumi A5 robotic injection press, characterized by its great precision, stability and rapid response during operation, or those of the Sandretto and Tederic, it is possible to produce a large quantity of pieces with various shapes. This allows us to have a very high and efficient production volume.
Soffiaggio HDPE
HDPE Blow molding is a technique that consists in obtaining hollow products in plastic material. The parts thus obtained, even very thin, allow for a high production volume with low costs.
The process consists of using a plastic preform inside a mold, modeled according to the shape you want to obtain, and compressed air is blown into the mold from the outside; in this way the preform will adhere to the walls of the mold itself and once the object is cooled and the mold is opened, the finished product will be ready for use.
For this technique, Iamtoys strictly uses handcrafted machinery of the highest quality.
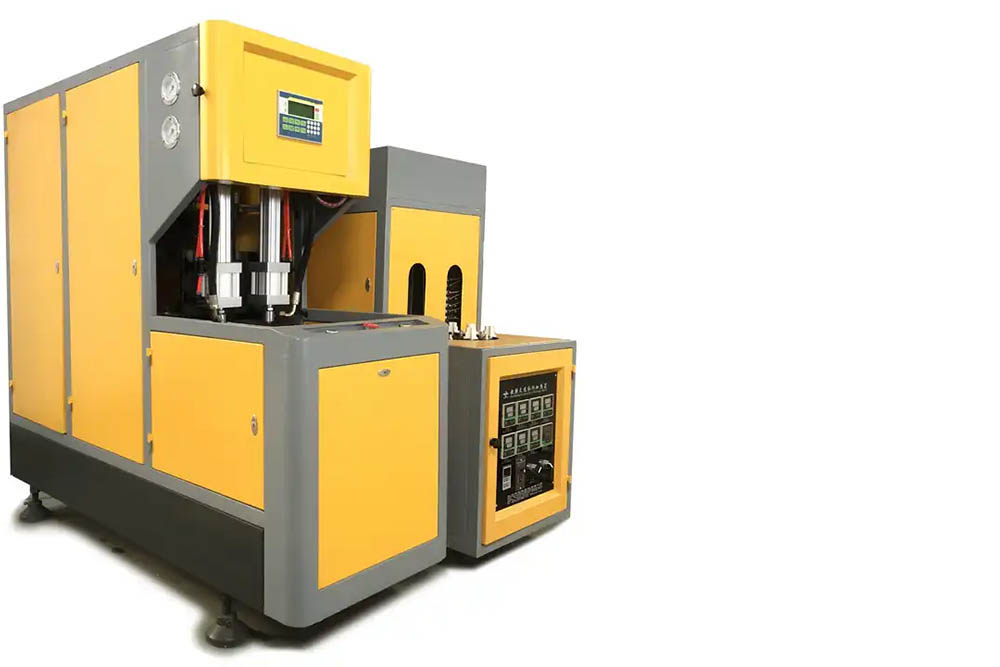